Vibratory finishing
Vibratory machining, also known as vibratory finishing or vibratory deburring, is a mechanical method used to efficiently and rapidly smooth, finish, and deburr metal parts. It requires putting the workpieces into a vibratory finishing machine together with abrasive media and a proper deburring compound. The machine vibrates at high frequencies, causing the media to contact with the pieces and remove material and round the edges.
The main advantages of vibratory machining include:
Deburring and edge rounding: Vibratory finishing process is especially useful for eliminating sharp edges (burrs) left on machined or laser-cut metal objects. This procedure guarantees that the edges of the parts are smooth and rounded, which is critical for preventing damage during assembly and use.
Consistent and uniform results: Vibratory machining provides consistent deburring and finishing across the whole batch. It ensures that all parts receive the same level of treatment, resulting in uniform quality.
Low labour consumption: Unlike hand deburring, which can be time-consuming and labor-intensive, vibratory finishing equipment can process a large number of components at once, minimising the requirement for physical labour and saving time.
Vibratory machining is versatile and can be used with a variety of materials, including non-ferrous metals, stainless metals, aluminium, and other non-ferrous alloys.
Rounded edges and deburred surfaces not only minimise damage during assembly, but they also improve the overall performance and longevity of the parts, particularly in applications where friction or wear may occur.
Cost-effectiveness: Because vibratory machining is automated, it eliminates the need for manual labour and specialised deburring tools, making it a cost-effective solution for finishing metal parts.
It’s important to note that choosing the right abrasive media and deburring compound is critical to getting the job done without damaging the parts. Furthermore, the processing duration and vibration intensity must be carefully managed to avoid over- or under-finishing the pieces.
Details
Capacity:
- 300kg
Medium:
- Stones
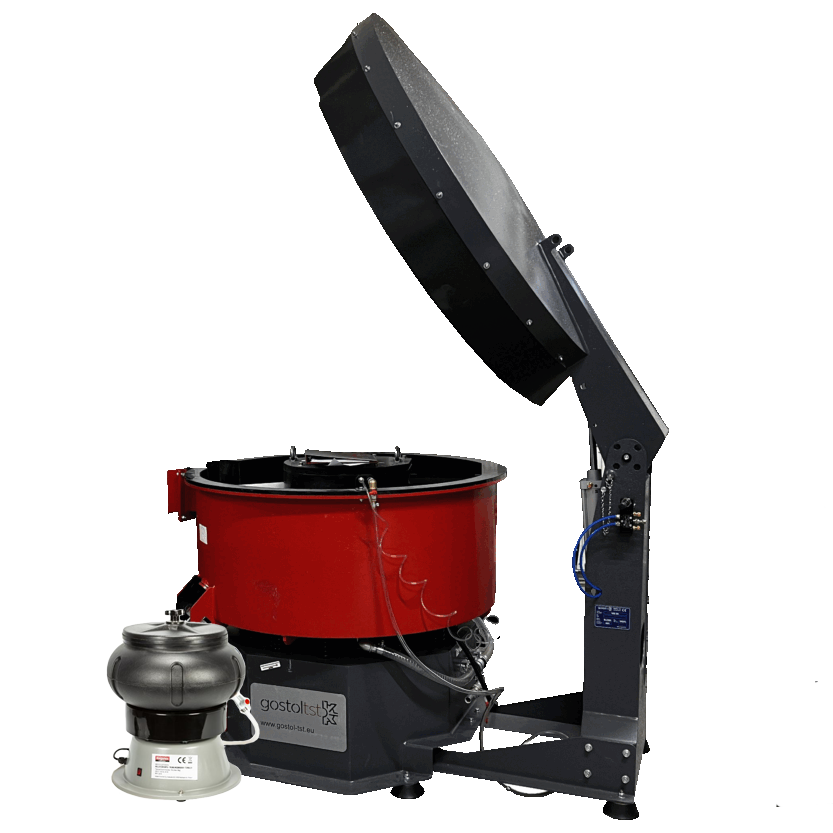